By understanding motor torque requirements and selecting the right mechanical features, it is possible to choose a motor that will last many years beyond a warranty period with minimal maintenance.
Selecting the right design
Industrial electric motors are critical for the successful operation of large conveyor systems.
The primary function of a motor is to produce torque, which is a function of power and speed. The National Electrical Manufacturers Association (NEMA) has design classification standards that identify the performance of different motors. These classifications are known as NEMA design curves, and there are typically four of them: A, B, C and D.
Each curve specifies the standard torque required to start, accelerate and operate different loads. NEMA design B motors are considered standard. They’re used for a variety of applications with slightly less starting current, where large start-up torque is not required and in instances where the motor does not need to support a large load.
While NEMA design B covers about 70 percent of all motors, other torque designs are sometimes necessary.
NEMA design A is similar to B, but with a higher starting current and torque. Design A motors are excellent for use with variable frequency drives (VFDs) because high-breakdown torque occurs when a motor is nearing full load and the higher inrush at start-up does not impact the performance.
NEMA design C and D motors are considered high-starting torque motors. These are used when more torque is needed earlier in the process in order to start a very heavy load.
The greatest difference between NEMA design C and D is the amount of slip in the final speed of the motor. The slip of the motor directly impacts the full load speed of the motor. A four-pole motor without slip would run at 1,800 rpm. That same motor with more slip would run at 1,725 rpm – or, less slip would be 1,780 rpm.
Most manufacturers provide a variety of stock motors designed for each of the different NEMA design curves.
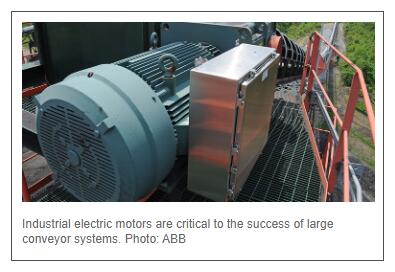
Motor torque curve characteristics
There are points of a motor curve that are critical when comparing the design curves:
• Locked rotor is also known as starting torque
• Pull-up torque is the minimum torque produced by a motor during start-up
• Breakdown torque is the maximum torque a motor will produce during start-up
• Full-load torque is the torque a motor will produce at rated power and speed
The amount of torque available at different speeds during the start-up process is important because of the demand of the application.
Conveyors are constant torque-load applications, meaning the torque they require is constant after start-up. Still, conveyors need additional torque at start-up before they can achieve constant torque operation. If a conveyor requires more torque than a motor can provide before start-up, other devices such as VFDs and fluid couplings allow for the full use of breakdown torque.
One phenomenon that could negatively impact the load starting is low voltage. If you have an input power voltage drop, the torque produced can be reduced significantly.
While considering if the motor torque is adequate to start the load, starting voltage needs to be considered. The relationship between voltage and torque is a square function. As an example, if the voltage drops to 85 percent during start-up, the motor will develop about 72 percent of the torque it would at full voltage. Be certain to evaluate motor starting torques versus load in worst-case conditions.